Common Welding Mistakes to Avoid for Safe and Strong Joints
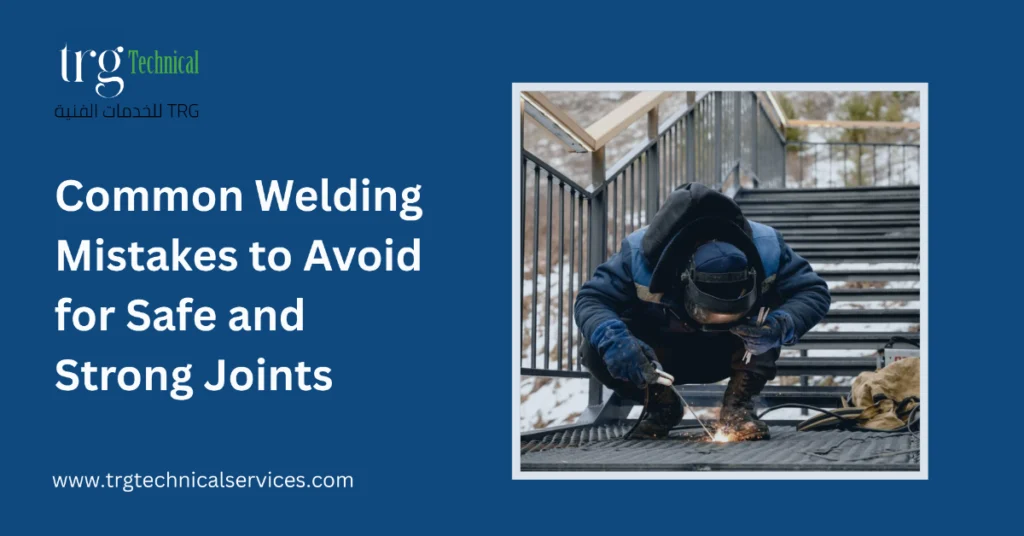
Welding is an important process in shipbuilding, manufacturing, construction, and millions of other industries. An effective weld guarantees structural strength, safety, and durable longevity. Professional welders, though, can commit errors that can disempower the joints and induce safety risks.
Recognizing and preventing these are the keys to ensuring that welds are strong, clean, and dependable. Whether you are an experienced professional or a newcomer, this guide will assist you in finding important areas for improvement and enhance the quality of weld work.
1. Incorrect Electrode or Filler Material Selection
One of the most basic welding errors is employing the wrong filler material or electrode for the application. Each material whether it is carbon steel, stainless steel, or aluminum—needs a compatible filler in order to have proper bonding and strength.
What to do instead:
Always consult the welding procedure specification (WPS) or material compatibility charts to select the proper consumables for the welding process and base metal.
2. Poor Surface Preparation
A clean surface is required for a good weld. Filth, oil, rust, paint, or water can dirty the weld area and cause porosity, poor joints, or full weld failure.
What to do instead:
Clean all surface dirt off with a wire brush, grinder, or chemical cleaner before welding. This provides better fusion and fewer defects.
Related: The Best Welding Materials for Long-Lasting Results
3. Incorrect Heat Input or Amperage Settings
Applying the incorrect amperage or heat input is a leading source of welding defects. Excessive heat burns through thin metal or creates excessive spatter, while inadequate heat provides poor penetration and weak fusion.
What to do instead:
Adjust the amperage according to the thickness, type, and position of material being welded. Conduct test welds on scrap to adjust amperage and voltage to a more precise setting.
4. Wrong Travel Speed
Travel speed is how quickly the electrode or torch travels along the joint. Moving too quickly can cause lack of fusion, undercut, or irregular beads. When moving too slowly, excessive heat causes warping or burn-through.
What to do instead:
Use a consistent, moderate travel speed suitable for the process and material. Repeated practice will build a steady hand and improved control.
Related: The Different Types of Welding and its Uses
5. Inadequate Joint Fit-Up or Alignment
Inadequate fit-up between pieces will result in gaps, misalignment, or insufficient welds. This is particularly undesirable for structural or pressure-bearing uses, where minor deviations will result in failure.
What to do instead:
Spend a moment clamping and aligning the workpieces correctly. Provide uniform joint gaps and inspect angles prior to striking the arc.
6. Ignoring Preheating or Post-Weld Treatment
Some metals, like high-carbon steel, must be preheated to prevent cracking. Post-weld heat treatment (PWHT) might also be needed to reduce residual stresses or enhance weld toughness.
What to do instead:
Understand the thermal needs of the materials you are working with. Apply an infrared thermometer or thermal chalk to check correct preheat temperatures and adhere to standard practice for post-weld treatments.
Related: Metal Fabrication Basics: What You Need to Know
7. Disregarding Safety Procedures
Welding without the use of proper PPE, ventilation, or fire preventative procedures can result in severe injuries. Arc flash, fumes, burns, and fires are all typical hazards in welding applications.
What to do instead:
Wear a certified welding helmet, gloves, and fire-resistant apparel at all times. Make sure the work area is ventilated and there are no flammable materials nearby. Adhere to OSHA or local safety regulations at all times.
8. Lack of Practice and Training
Most welding mistakes are due to inexperience or a lack of training. Skipping the learning curve or overconfidence can lead to substandard welds and eventual failure.
What to do instead:
Invest in on-the-job training, welding certifications, or hands-on training. Even experienced welders need to practice regularly and improve continuously.
Related: How Welding Services Can Benefit Your Construction Projects
Why It Matters: The Cost of a Bad Weld
A poorly welded joint doesn’t only appear unsightly it can be dangerous. In oil and gas, aviation, and structural steel industries, weld failure can have disastrous consequences, ranging from property damage to production downtime, and even loss of life.
Here at TRG Technical Service, we’ve witnessed how the right welding practices can make projects better, safer, and more durable. That’s why we focus on precision and professionalism in each and every welding work we undertake.
TRG Technical Service: Your Welding Experts in Pakistan
TRG Technical Service offers comprehensive welding solutions tailored to meet the needs of industries across Pakistan. From structural welding and pipeline joints to specialized fabrication, our certified welders ensure each job meets international standards.
We provide:
- Certified welding personnel
- On-site and in-house welding services
- Weld inspection and testing
- Repair and maintenance welding
- Material consultation and procedure development
With a focus on quality, safety, and reliability, we’re committed to delivering welds that last.
Get in Touch
Whether you’re facing weld quality issues or need expert support for your next project, TRG Technical Service is here to help.
Contact us today to learn more.
Phone: +971 501704507
Email: info@trgtechnicalservice.com
Website: www.trgtechnicalservice.com